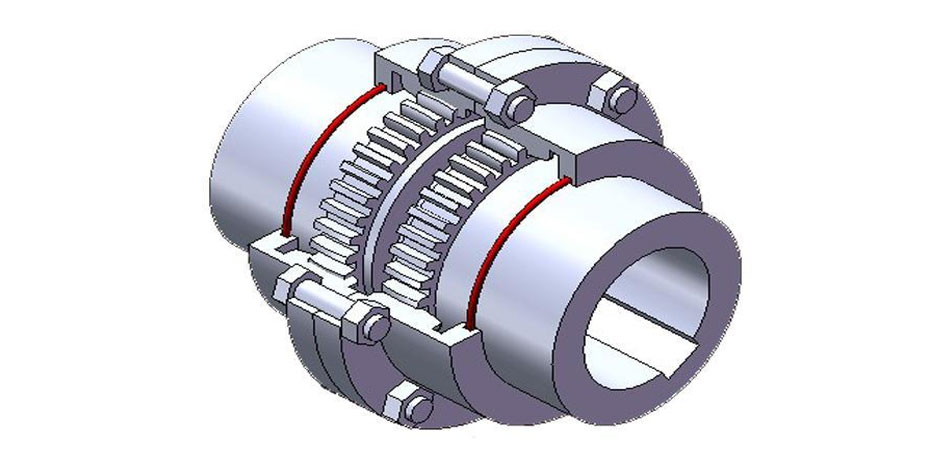
--Ingiant Technology Industry News
In the vast world of mechanical engineering, there is a component that is like an invisible bridge, silently supporting the operation of countless machines - this is the slip coupling. It not only connects two shafts, but also transmits power and torque, and is an indispensable part of mechanical equipment. Today, I will take you into the world of slip couplings and explore its mysteries together.
Overview of Copper Slip Couplings
The copper slip coupling is a special type of coupling, famous for its unique material selection. Copper is selected as the main material not only because of its good electrical conductivity, which is particularly important in certain specific applications such as motor drive systems, but also because copper has high corrosion resistance and wear resistance. In addition, copper couplings are usually used in occasions that require good thermal conductivity, such as equipment transmission in high temperature environments. This material selection enables the copper slip coupling to maintain stable performance under harsh working conditions, providing reliable protection for industrial production.
Working Principle
The core working principle of the slip coupling is based on the action of friction. When the active shaft starts to rotate, it drives the middle slider to move through friction, and then drives the driven shaft to follow the rotation. During this process, the slider can slide freely between the two half-couplings, allowing a certain degree of axis deviation without affecting normal operation. It is worth noting that although the slider allows relative movement within a certain range, in order to maintain the stability of the system, these deviations must be strictly controlled not to exceed the limits specified by the manufacturer.
Types of sliding couplings
The sliding coupling family has many members, each with its own advantages. According to different application scenarios and technical requirements, it can be divided into several common types:
- Slider coupling: It consists of two sleeves and a center slider, which is suitable for low speed and large torque transmission. The center slider is usually made of engineering plastics or metal, which can effectively compensate for the relative displacement between the two shafts and ensure backlash-free operation. Although the slider may wear out over time, it is inexpensive to replace and easy to maintain
- Cross slider coupling: The middle slider is square in design, and the radial grooves on the end faces of the two half-couplings are used to achieve sliding connection. Compared with ordinary slider couplings, cross slider couplings are noisier and less efficient, but they still have their place in specific low-speed scenarios.
- Plum blossom elastic coupling: It absorbs vibration and reduces impact loads through specially shaped elastomers, which is suitable for occasions with high precision positioning requirements. When installing, it is necessary to ensure the appropriate distance between the two sleeves to prevent damage caused by direct metal contact.
Importance of materials
Material selection is crucial for sliding couplings. In addition to the copper mentioned above, there are many other materials to choose from, such as 45 steel for high-strength parts, which can significantly increase hardness after heat treatment; and for those applications that do not require high precision but want to reduce costs, you can choose more economical options such as Q275 steel. In addition, in order to reduce the coefficient of friction and extend the service life, many sliding couplings will add lubricating oil for lubrication. The right material combination can not only enhance the durability of the product, but also improve the overall performance
Typical Application
Data transmission for industrial rotating equipment
For high-speed rotating industrial equipment, traditional slip ring technology faces many challenges, such as wear, maintenance requirements, and sensitivity to electromagnetic interference. To address these issues, some manufacturers have developed 60 GHz wireless data interconnection-based technologies to replace traditional contact interfaces. This new solution enables reliable data transmission while maintaining high rotation speeds and is not affected by physical misalignment, EMI (electromagnetic interference), crosstalk, and contaminants. In addition, the technology supports a variety of communication protocols, including IEEE802.3 standard Ethernet, ensuring good compatibility and scalability.
If you want to know more about our product technical, you can click ingiant slip ring here.
Pre-installation preparation
Before starting the installation, the first thing to do is to ensure that all preparations are ready. This includes but is not limited to:
- Check component integrity: Confirm that the coupling and its various components are not damaged or defective, such as for cross slider couplings, make sure that the slider surface is smooth and free of cracks or wear.
- Clean the ends of the connecting shafts: Remove any oil, dust or other impurities that may affect the installation accuracy, which is essential to ensure a good mechanical fit.
- Measurement and verification: Use appropriate tools to measure parameters such as diameter, length and centering deviation of the two shafts to ensure that the selected coupling is suitable for the two shafts and provide a basis for subsequent installation adjustments.
Installation steps
For cross slider couplings
- Install the half couplings: Install the two half couplings on the corresponding shafts respectively, and fix them with keys or set screws to ensure that they are firmly and reliably connected to the shafts.
- Place the slider: Place the cross slider into the groove of one of the half couplings, paying attention to the correct direction so that it can slide freely in the groove.
- Docking the coupling: Slowly move the other half coupling closer so that the slider can smoothly enter the other side's groove. Keep the two shafts parallel during the process to avoid applying unnecessary lateral force.
- Fix the coupling: Install the connecting bolts and fix the two half couplings together. When tightening the bolts, follow the diagonal order to gradually and evenly apply force.
- Accuracy check: Finally, carefully check the installation accuracy of the coupling, including centering deviation and axial clearance, and adjust if necessary to ensure that it meets the requirements
For roller chain coupling
- Install the sprocket: First install the sprocket on the driving shaft and the driven shaft, ensuring that the sprocket fits tightly with the shaft and is fixed by key or other means.
- Install the chain: Put the chain on the sprocket, pay attention to the direction matching, and adjust the chain tightness to a moderate level, neither too loose nor too tight.
- Adjust the position: Reduce the axial and radial deviation between the two shafts by moving the shaft or adjusting the position of the coupling, which can be assisted by tools such as rulers and dial indicators.
- Tighten the connections: Install and tighten all the connections of the coupling, and cross-tighten the bolts according to the specified torque value to ensure the safety and reliability of the connection.
- Final inspection: After completing the above steps, check the tightness of the chain, the alignment of the two shafts, and whether all the connections are tightened in place.
Post-installation inspection
After installation, a series of tests are required to ensure that the coupling can work properly:
- Manual rotation test: Gently rotate the two shafts by hand to observe whether the coupling rotates smoothly and whether there is any jamming.
- Low-speed test run: Start the equipment and run it at a lower speed for a period of time to monitor whether the coupling has abnormal vibration, heating, etc. If a problem is found, stop the machine immediately to investigate the cause and solve it.
Frequent Issue Examination
Even with careful design and installation, sliding couplings may encounter some challenges. Here are some common problems and their solutions:
- Abnormal noise: If you hear unusual sounds, it may be due to lack of lubrication or severe wear of the slider. Regular addition of lubricating oil and timely replacement of worn parts can help solve the problem.
- Premature failure: When the coupling is found to fail prematurely, you should consider whether there is an axial deviation beyond the allowable range. Precisely adjusting the axis alignment can effectively extend the service life.
- Too high temperature: If the temperature in the coupling area rises abnormally, this is usually due to heat accumulation caused by excessive friction. Check whether there are adequate cooling measures and ensure that the pressure between the slider and the sleeve is moderate
In short, the sliding coupling is not only an important part of the mechanical transmission system, but also a manifestation of the wisdom of engineers. Through in-depth understanding of different types, reasonable material selection and standardized installation processes, we can better play their advantages and contribute to the development of modern industry. I hope this article will give you a deeper understanding of the sliding coupling, and you are also welcome to interact with us to share your own experience and insights. Let us witness the continuous progress and development of this field together
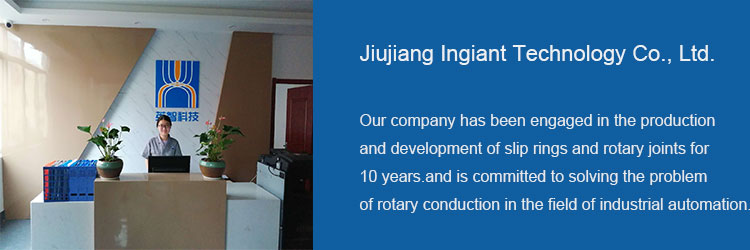
Post time: Dec-28-2024